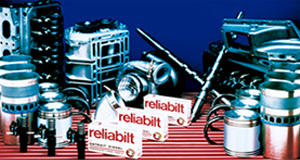 
The brand name for factory remanufactured parts.
Not rebuilt, but completely remanufactured to original BluePrint specifications.
Philosophy
The objective in remanufacturing is to return the parts or complete engine to new specifications and upgrade it with the latest engineering changes… a big difference from the rebuilder’s objective of making a component work again.
Advantages
- Component Cleaning Edge
- Cost Advantage
- Engineering Edge
|
- Equipment Edge
- Information Edge
- Quality
|
- Maximum Uptime
- Newest Technology
- No-Hassle Core Acceptance
|
- Remanufacturing Edge
- Warranty
|
Means More
New |
Remanufactured |
- Bearings
- Clamps
- Dampers
- Filters
- Fittings
- Gaskets
- Harnesses
- Hoses
|
- Liners
- Oil Cooler Cores
- Pistons
- Seals
- Sensors
- Vibration
- Wiring
|
- Air Compressor
- Alternator
- Camshaft
- Connecting Rods
- Crankshaft
- Cylinder Head
|
- Electronic Unit Pump
- Fuel Pump
- Nozzle
- Turbocharger
- Water Pump
|
Newest Technology
- DDC and Mercedes Benz Blueprints are proprietary information and not shared with outside parties.
- Engineering change notices are only know through DDC engineers and staff.
- Material specifications are kept proprietary to protect DDC Genuine quality.
Engineering Edge
- Dedicated Component Development Engineers
- Dedicated Manufacturing Engineers
- Dedicated Quality Managers
- Support from Original Development Engineers at Mercedes Benz, Germany, DDC & MTU-DD Detroit
- Durability & Performance Tests in Engineering Lab to Validate Design
- Application of Detroit’s Engineering Book of Knowledge
- Warranty Background
- Design Sensitivities
Quality
The Remanufacturing Process
- Engine disassembled and sorted by component
- Components are cleaned
- Components are inspected and gauged
- Parts are remanufactured if applicable
- Tested using same procedures and specifications as OEM production
- Upgraded with critical design improvements
Component Cleaning Edge
Bake Oven
- Bake Oven Process Provides Stress Relief and Cleaning Benefits
- 800°f For Cast Iron
- 600°f For Aluminum
|
|
Shot Blasting
Shot blasting consists of attacking the surface of a material with one of many types of shots. Normally this is done to remove something on the surface such as scale, but it is also done sometimes to impart a particular surface to the object being shot blasted. The shot can be sand, small steel balls of various diameters, granules of silicon carbide, etc. The device that throws the shot is either a large air gun or spinning paddles which hurl the shot off their blades. |
Equipment Edge
reliabilt Parts – The right equipment for the job:
- Coordinate Measuring Machine (CMM)
- Computer Numerical Controlled Machining Center (CNC)
- Crankshaft Grinders
- Injector Calibrators
- Journal Honing Machine
- Specialty Measurement Gauges
DDC Reman uses a computer numerical controlled (CNC) coordinate measuring machine (CMM) to measure part features such as holes, cones, arcs, spheres, surfaces, etc., Features which can not be measured with conventional hand tools are easily measured to a high degree of precision with the CMM. Reman centers are DDC Business Units Due to DDC’s commitment to quality we invest substantial capital into specific equipment that rebuilders are normally unable to acquire, leaving them left to very simple tools.
Information Edge
reliabilt Parts – Full access to factory blueprints, change notices, and material specifications.
Other "Rebuilt" Parts – Limited access to proprietary specifications.
Remanufacturing Edge
- Spray Welding is a remanufacturing process in which molten/powered metal is sprayed onto metal surfaces to bring them to new specifications.
- Updates are the beauty of hindsight, where field experienced parts are brought to the latest design level.
- Conversions allows DDC to have an easy core acceptance because they can take parts, such as shared castings, that are no longer current and remanufacture them to the latest blueprint specifications.
ISO 9002 Certified
- Latest engineering specifications are being used
- All processes meet product engineering requirements
- All gages are calibrated regularly to assure accuracy
- All gages are verifiable to national standards
- All products are inspected using the correct gages
- All remanufacturing operations are documented and controlled
- The workforce is properly selected and trained
- All customer feedback is evaluated and utilized
- An organized and effective corrective action system is being used
- The entire workforce understands the quality policy and objectives
- Communication is effective throughout the organization
|